The static error sources of Coordinate Measuring Machine mainly include: the error of the Coordinate Measuring Machine itself, such as the error of the guiding mechanism (straight line, rotation), the deformation of the reference coordinate system, the error of the probe, the error of the standard quantity; the error caused by various factors associated with the measurement conditions, such as the influence of the measurement environment (temperature, dust, etc.), the influence of the measurement method and the influence of some uncertainty factors, etc.
The error sources of coordinate measuring machine are so complicated that it is difficult to detect and separate them one by one and correct them, and generally only those error sources that have a great influence on the accuracy of coordinate measuring machine and those that are easier to separate are corrected. At present, the most researched error is the mechanism error of coordinate measuring machine. Most of the CMMs used in production practice are orthogonal coordinate system CMMs, and for general CMMs, the mechanism error mainly refers to the linear motion component error, including positioning error, straightness motion error, angular motion error, and perpendicularity error.
To evaluate the accuracy of the coordinate measuring machine or to implement error correction, the model of the inherent error of the coordinate measuring machine is used as the basis, in which the definition, analysis, transmission and total error of each error item must be given. The so-called total error, in the accuracy verification of CMMs, refers to the combined error reflecting the accuracy characteristics of CMMs, i.e., the indication accuracy, the repetition accuracy, etc.: in the error correction technology of CMMs, it refers to the vector error of spatial points.
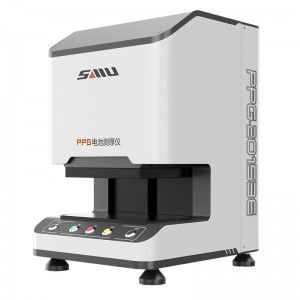
Mechanism error analysis
The mechanism characteristics of CMM, the guide rail limits five degrees of freedom to the part guided by it, and the measurement system controls the sixth degree of freedom in the direction of motion, so the position of the guided part in space is determined by the guide rail and the measurement system to which it belongs.
Probe error analysis
There are two types of CMM probes: contact probes are divided into two categories: switching (also known as touch-trigger or dynamic signaling) and scanning (also known as proportional or static signaling) according to their structure. Switching probe errors caused by the switch stroke, probe anisotropy, switch stroke dispersion, reset dead zone, etc.. Scanning probe error caused by the force a displacement relationship, displacement a displacement relationship, cross-coupling interference, etc..
The switching stroke of the probe for the probe and workpiece contact to the probe hair hearing, the probe deflection of a distance. This is the system error of the probe. The anisotropy of the probe is the inconsistency of the switching stroke in all directions. It is a systematic error, but usually treated as a random error. The decomposition of the switch travel refers to the degree of dispersion of the switch travel during repeated measurements. The actual measurement is calculated as the standard deviation of the switch travel in one direction.
Reset deadband refers to the probe rod deviation from the equilibrium position, remove the external force, the rod in the spring force reset, but due to the role of friction, the rod can not return to the original position, it is the deviation from the original position is the reset deadband.
Relative integrated error of CMM
The so-called relative integrated error is the difference between the measured value and the true value of the point-to-point distance in the measurement space of CMM, which can be expressed by the following formula.
Relative integrated error = distance measurement value a distance true value
For CMM quota acceptance and periodic calibration, it is not necessary to know precisely the error of each point in the measurement space, but only the accuracy of the coordinate measurement workpiece, which can be assessed by the relative integrated error of the CMM.
The relative integrated error does not directly reflect the error source and the final measurement error, but only reflects the size of the error when measuring the dimensions related to the distance, and the measurement method is relatively simple.
Space vector error of CMM
Space vector error refers to the vector error at any point in the measurement space of a CMM. It is the difference between any fixed point in the measurement space in an ideal right-angle coordinate system and the corresponding three-dimensional coordinates in the actual coordinate system established by the CMM.
Theoretically, the space vector error is the comprehensive vector error obtained by vector synthesis of all errors of that space point.
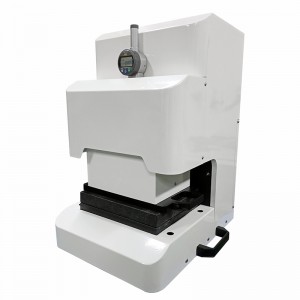
The measurement accuracy of CMM is very demanding, and it has many parts and complex structure, and many factors affecting the measurement error. There are four main sources of static errors in multi-axis machines like CMMs as follows.
(1) Geometric errors caused by the limited accuracy of structural parts (such as guides and measuring systems). These errors are determined by the manufacturing accuracy of these structural parts and the adjustment accuracy in installation and maintenance.
(2) Errors related to the finite stiffness of the mechanism parts of the CMM. They are mainly caused by the weight of the moving parts. These errors are determined by the stiffness of the structural parts, their weight and their configuration.
(3) Thermal errors, such as expansion and bending of the guide caused by single temperature changes and temperature gradients. These errors are determined by the machine structure, material properties and temperature distribution of the CMM and are influenced by external heat sources (e.g. ambient temperature) and internal heat sources (e.g. drive unit).
(4) probe and accessory errors, mainly including changes in the radius of the probe end caused by the replacement of the probe, the addition of a long rod, the addition of other accessories; anisotropic error when the probe touches the measurement in different directions and positions; the error caused by the rotation of the indexing table.
Post time: Nov-17-2022